Hard Chrome Plating Training Course
Appendix 6. Amps Vs. Volts
Amps vs. Volts
When you chrome plate, you can adjust the rectifier using either the amperage or voltage controls. Experts have been arguing about which is better since the chromium process was first commercialized around 1925. The truth is, there is no universal best way. It really depends on what you are plating and the equipment you are using.
In any case, it is a good idea to know how to plate both by amps and by volts. You might have process instructions that require you to plate by one method or the other, so you need to be prepared to deal with either one. Once you get a feel for the relationship between amps and volts, you will be a better chrome plater.
First, we will say a few words about understanding amps and volts. Then we will see how to plate a typical part, first by using amperage control, and then by using voltage control.
Before we start plating, let's get a picture of what amps and volts really measure. Think of water flowing through a pipe. There are two important quantities to know if you want to control the flow. You want to know how many gallons a minute are flowing, and you want to know how much pressure there is pushing the water through the pipe.
That same picture works for electricity flowing through a wire. Amperage tells you how much electricity is flowing, and
voltage tells you how much electrical pressure is pushing it.
It's important to realize that, even though amps and volts are related to one another, you can set them separately
on most rectifiers. Let's see how this works.
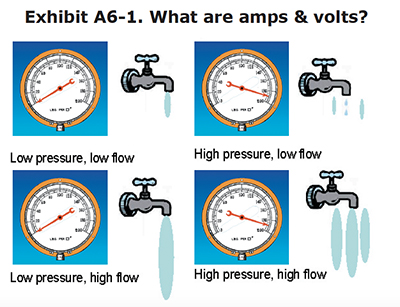
Take the case of water flowing through a pipe (Exhibit A6-1). You know that pressure and flow are related. If you open the faucet a certain amount and leave it there, then increasing the pressure will increase the flow. But you can still set them separately, by opening or closing the faucet. If the water pressure is high, closing the faucet slightly will produce a low flow, and opening it more will produce a high flow. The same is true if the water pressure is low. In that sense, pressure and flow can be set independently.
Volts and amps act the same way. By opening or closing an electrical "faucet" – in other words, by changing the resistance in the electric circuit -- you can set volts and amps independently. That's essentially what the separate voltage and amperage controls on the rectifier allow you to do. The voltage control lets you turn up the pressure, and the amperage control lets you open the faucet.
Plating by Amperage
First, let's learn how to plate by amperage. When you set the amperage, you tell the rectifier "This is how much current I want flowing. The rectifier's job is to make it happen." The rectifier will then automatically adjust the "electrical pressure" – the voltage – in order to produce the flow you requested.
So how do you decide how much current you want flowing? Well, that depends on the area that you're plating. What counts is how much current is flowing in every square inch of exposed surface – the so-called "current density." Double the number of square inches, and you're going to want to double the amount of current to keep the whole surface plating at the right rate. So to set the current, you need to know two things: what current density to use, and how much area you're plating.
For chrome plating, it turns out that a current density of 3 amps per square inch is a good place to start. Let's say you are going to be plating three pistons at the same time, and that each piston has an area of 10 square inches. In that case, your total area would be 3 times 10, or 30 square inches. If you want to plate at 3 amps per square inch, then the rectifier needs to provide 3 amps per square inch times 30 square inches, or 90 amps.
Next we need to tell the rectifier to deliver 90 amps. For now, let's assume that the parts have already been reversed etched.
Start with the rectifier voltage and amperage controls at the zero positions. Then set the voltage control to 100
percent. That tells
the rectifier that it's free to provide as much voltage as necessary. But even though the voltage control is set at
100%, the voltage meter will still read zero, since you're asking for zero current.
Now adjust the amperage control until you get a reading of 90 amps (Exhibit A6-2). You will notice that the voltage meter goes up as you increase the amperage. The rectifier is automatically increasing the voltage until it is delivering the current you want. In this typical case, when the current has reached 90 amps, you will see that the voltage reading has increased to 4.2 volts.
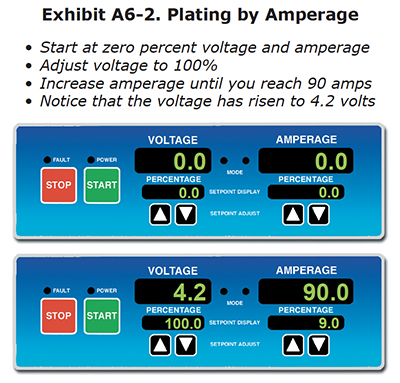

Plating by Voltage
Now let's start over again. But this time, let's control the voltage, rather than the amperage.
When you use voltage to control the process, you don't necessarily need to know the area to be plated. You just need to know what voltage setting to use. Later we will discuss which factors to consider when selecting a voltage setting. For now, let's assume that the instructions for the pistons tell you to use 4.2 volts.
As we did before, let's assume that the parts have already been reversed etched.
Start with the rectifier voltage and amperage at the zero position (Exhibit A6-3). Then, raise the amperage to 100 percent. In this case, you're telling the rectifier to allow any value of current that it can deliver. But, of course, the amperage meter will still read zero, since the voltage control is still set at zero. No pressure, no flow.
Now adjust the voltage control until you get a reading of 4.2 volts. You will notice that the amperage meter goes up as you increase the voltage. If you are plating the same pistons in the same bath as in the previous case, then the 4.2 volts of "electrical pressure" will produce an amperage reading of 90 amps, exactly as before.
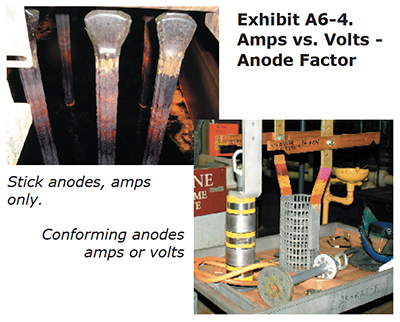
So now that we have a choice, how do we decide which method is better? One very important factor in this decision is the type of equipment you are using. Here is a simple rule: If you are plating with stick anodes, you should always plate by amperage. If you are plating with conforming anodes, you can plate by amperage or voltage (Exhibit A6-4).
Why is this true? It turns out that a very important factor in the relationship between volts and amps is the distance between the part being plated and the anode. If you are trying to water a patch of lawn with a garden hose, you're going to need more pressure if you want to reach a patch that is further away. The same is true with electric current. The greater the distance between the anode and the part you're plating, the more voltage is needed to deliver a given amount of amperage.
For example, if we were to plate the three pistons with stick anodes at a distance of six inches away, the voltage would have to be higher then if we used a conforming anode and the anode to cathode distance was only one inch.
With stick anodes it is difficult to always get the same anode to cathode distance for every part. Therefore, since the anode to cathode distance is variable, you cannot rely on getting the same amperage reading when you set the voltage.
On the other hand, conforming anodes often have the same anode to cathode distance. That means there is one less
variable to worry about and the relationship between amps and volts is pretty constant.
We will look at the distance factor more closely in the next discussion.
Anode to Cathode Distance Experiment
Exhibit A6-5 shows the results of a hypothetical experiment. For this experiment, we set up a set of eight stick anodes to plate a single piston. We started the plating process with an anode to cathode distance of four inches. Then, we moved the anodes away from the part so that the distance was about 6 inches and then moved them again so that it was about 12 inches. After each move, we adjusted the amperage so that we always had a 50 amp setting on the rectifier.
Look at what happened. At four inches we needed 5.5 volts to plate at an amperage of 50 amps. Once we moved the anodes six inches away from the part, and reset the amperage to 50 amps, then the voltage was 6.1 volts. And when we moved the anodes 12 inches away from the part, and reset the amperage to 50 amps, then the voltage was 6.9 volts.
This experiment proves that as the anode to cathode distance increases, it takes more voltage to plate at a given amperage.
With stick anodes it is difficult to always have the same anode to cathode distance. Therefore, you should not plate by voltage with stick anodes; you must rely on amperage.
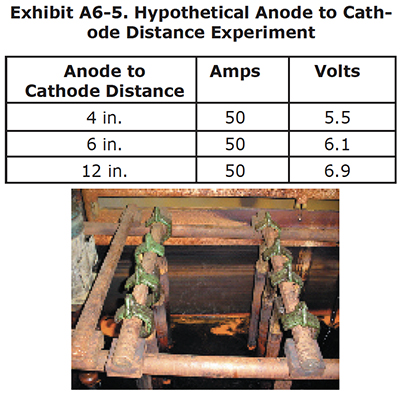
Plating by Voltage with Conforming Anodes
Here we have three different parts to plate and we are going to use conforming anodes. In each case, the distance between the cathode and anode is 3/4 inch.
Because the anode to cathode distance is constant, we can plate by amperage or voltage. Let's plate by voltage.
Start with the rectifier voltage and amperage controls at the zero positions. Then, adjust the amperage control to 100 percent and then adjust the voltage control until you get a reading of 4.2 volts. You will notice that the amperage meter goes up as you increase the voltage. In this case, the amperage reading is 120 amps.
Just for fun, let's figure out the current density at which we are now plating. As it turns out, the three parts have a surface area of 34 in2. Therefore, the current density is 120/34 or about 3.5 amps per square inch (APSI). That's a sweet spot for conforming anodes. We will probably get about 1.2 mils thick per hour and end up with a nice bright deposit.
Making the Decision
When you are using stick anodes, it is best to plate by amperage. If you are using conforming anodes, you can plate by amperage or voltage.
A plater does not always get to decide if they are going to plate by amps or volts, usually this is decided by management. In any case, hopefully this lesson has given you some information that you can use.
Perhaps what is most important in this lesson is that a chrome plater should be aware of both amps and volts, no mater what type of anodes are being used. Once you get some experience of checking both amps and volts, you get a sense for what readings to expect. If unexpected readings occur, then you know something is wrong and you can investigate it before you mis-plate a part.